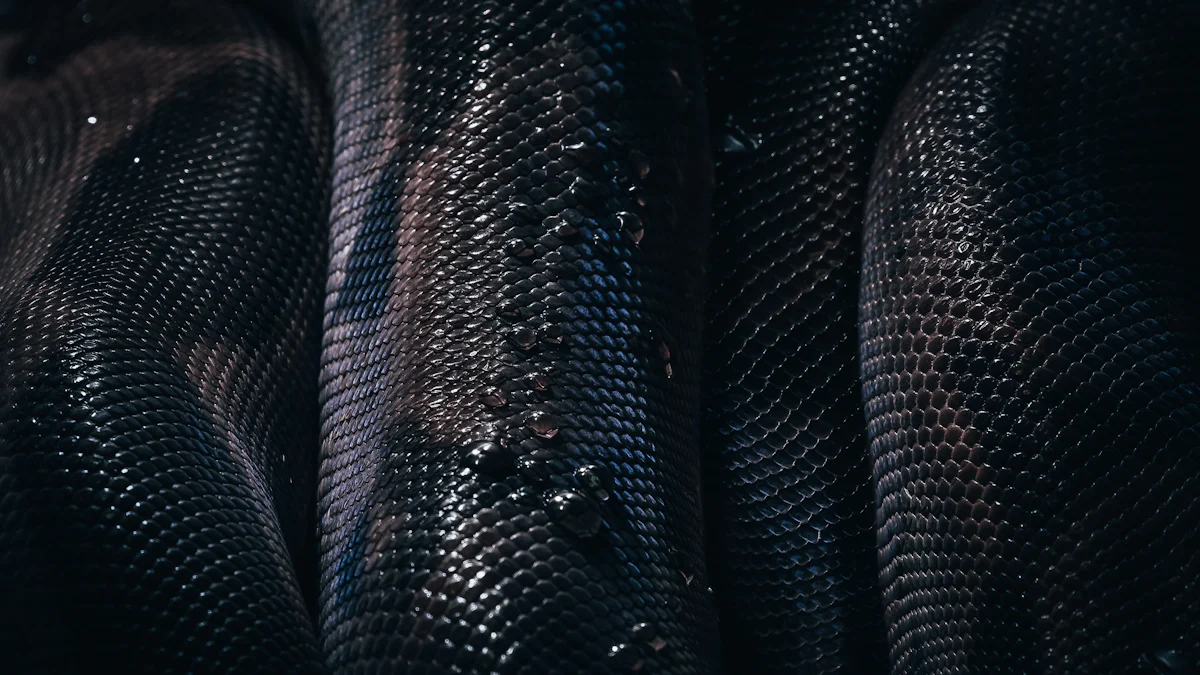
Carbon Fiber aero has revolutionized various industries due to its exceptional strength-to-weight ratio and durability. The global carbon fiber market reached a value of USD 4.66 billion in 2022, with significant growth expected in the coming years. Two primary types of carbon fiber aero exist: dry and wet carbon fiber. Understanding the differences between these types is crucial for selecting the appropriate material for specific applications. Each type offers unique advantages and disadvantages that impact performance, cost, and manufacturing complexity.
Basics of Carbon Fiber
What is Carbon Fiber?
Composition and Structure
Carbon fiber consists of thin filaments of carbon atoms bonded together in a crystalline structure. This arrangement results in an exceptional strength-to-weight ratio. The material is extremely stiff, strong, and light. Carbon fiber offers benefits such as high stiffness, high tensile strength, high-temperature tolerance, low thermal expansion, and high chemical resistance. Manufacturers often bundle these fibers together and weave them into a cloth. Combining this cloth with resin epoxy produces a strong and lightweight material.
Common Uses
Carbon fiber finds applications in various industries due to its unique properties. In aerospace, it is used for constructing aircraft components. The automotive industry utilizes carbon fiber for manufacturing high-performance vehicle parts. Sports equipment manufacturers use carbon fiber to produce bicycles, tennis rackets, and other sporting goods. Wind turbines also incorporate carbon fiber to enhance efficiency and durability.
Importance in Modern Industries
Automotive
The automotive industry benefits significantly from carbon fiber. High-performance vehicles use carbon fiber to reduce weight while maintaining structural integrity. Everyday cars also incorporate carbon fiber components to improve fuel efficiency and safety. Carbon fiber aero parts enhance vehicle aerodynamics, contributing to better performance.
Aerospace
In the aerospace industry, carbon fiber plays a crucial role. Aircraft manufacturers use carbon fiber to construct lightweight yet strong components. This reduces overall weight, leading to improved fuel efficiency and reduced emissions. Spacecraft also rely on carbon fiber for its high strength and durability under extreme conditions.
Sports Equipment
Sports equipment manufacturers leverage carbon fiber for its superior properties. Bicycles made from carbon fiber are lightweight and strong, providing better performance for cyclists. Tennis rackets and other sporting goods benefit from carbon fiber’s high stiffness and strength, enhancing the athlete’s performance.
Dry Carbon Fiber
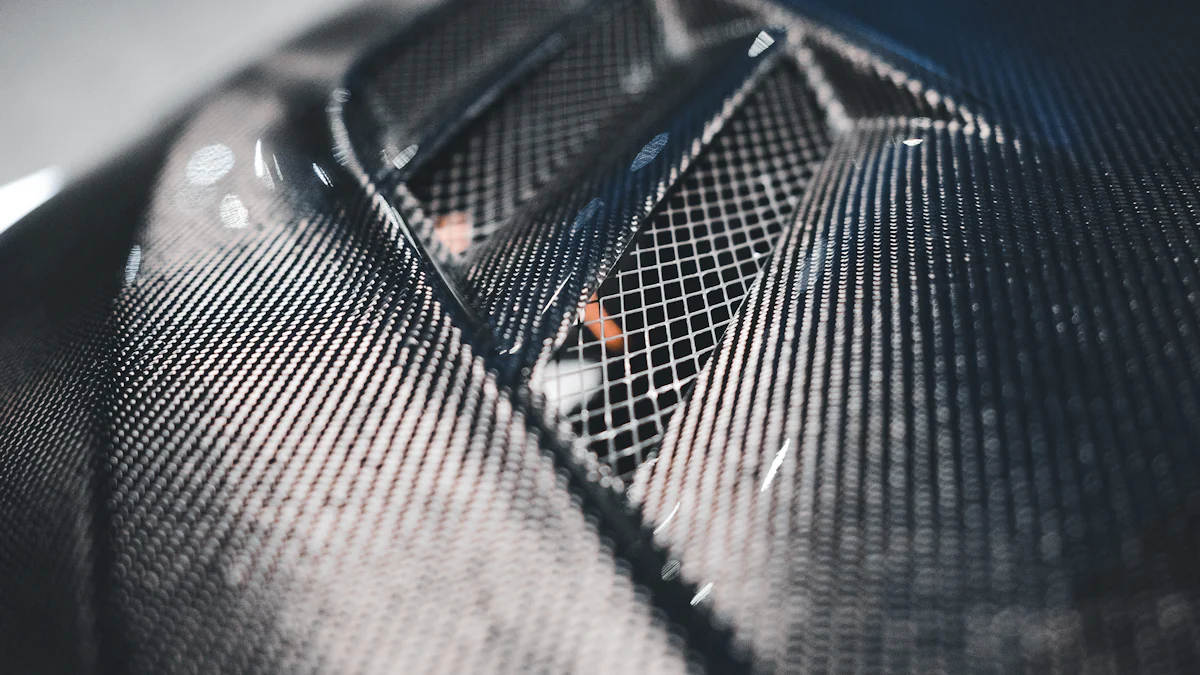
Manufacturing Process
Pre-impregnation with Resin
Manufacturers create dry carbon fiber by pre-impregnating carbon materials with resin. The resin is already integrated into the carbon fibers before any molding occurs. This process ensures that each fiber is uniformly coated with resin, enhancing the material’s overall quality. The pre-impregnated fibers are then placed into a mold, ready for the next step.
Curing Process
The curing process involves placing the pre-impregnated carbon fibers in a sealed vacuum. This environment eliminates air bubbles and ensures an even distribution of resin throughout the material. The vacuum-sealed mold is then subjected to heat, which activates the resin and hardens the carbon fiber. This method results in a high-quality, lightweight product with minimal waste.
Characteristics
Strength and Durability
Dry carbon fiber exhibits exceptional strength and durability due to its uniform resin distribution. The pre-impregnation process ensures that each fiber is coated evenly, reducing weak points and enhancing the material’s structural integrity. This makes dry carbon fiber ideal for applications requiring high strength and long-lasting performance.
Weight Considerations
Dry carbon fiber is known for its lightweight properties. The precise control over resin application minimizes excess weight, making it a preferred choice for industries where weight reduction is crucial. This characteristic contributes to improved fuel efficiency in automotive and aerospace applications.
Advantages
High Performance
Dry carbon fiber offers high performance due to its superior strength-to-weight ratio. The material’s consistent quality and structural integrity make it suitable for high-stress applications. Industries such as aerospace and automotive benefit from the enhanced performance characteristics of dry carbon fiber.
Consistency in Quality
The manufacturing process of dry carbon fiber ensures consistency in quality. The pre-impregnation and vacuum-sealed curing process result in a uniform product with minimal defects. This consistency is critical for industries that demand reliable and predictable material properties.
Disadvantages
Cost
Dry carbon fiber production involves significant expenses. The pre-impregnation process requires specialized equipment and materials. High-quality resin and carbon fibers contribute to the overall cost. The curing process in a sealed vacuum adds further to the expense. Industries must consider these costs when opting for dry carbon fiber.
Complexity in Manufacturing
The manufacturing process of dry carbon fiber is complex. Pre-impregnating carbon materials with resin demands precision. Any deviation can affect the quality of the final product. The curing process in a vacuum-sealed environment requires meticulous control. This complexity can lead to longer production times. Manufacturers need skilled labor and advanced technology to maintain consistency.
Wet Carbon Fiber
Manufacturing Process
Resin Application
Wet carbon fiber involves applying resin directly to the carbon fabric. Manufacturers use a hand-coating technique to ensure the resin thoroughly saturates the fibers. This process allows for flexibility in the amount of resin used, accommodating various application needs.
Lay-up and Curing
After resin application, the carbon fabric undergoes a lay-up process. Technicians layer the resin-coated fabric into molds, shaping it to the desired form. The curing process follows, where the material hardens at room temperature or under heat. This step solidifies the structure, making it ready for use.
Characteristics
Flexibility in Application
Wet carbon fiber offers significant flexibility in its application. The hand-coating method allows for adjustments in resin quantity, making it suitable for complex shapes and custom designs. This adaptability proves beneficial in industries requiring tailored solutions.
Weight Considerations
Wet carbon fiber tends to be heavier than dry carbon fiber. The manual resin application can lead to excess resin, increasing the overall weight. Despite this, wet carbon fiber remains a viable option for applications where weight is less critical.
Advantages
Cost-Effectiveness
Wet carbon fiber stands out for its cost-effectiveness. The production process uses cheaper materials and equipment, reducing overall expenses. This affordability makes wet carbon fiber an attractive choice for budget-conscious projects.
Simplicity in Manufacturing
The manufacturing process of wet carbon fiber is relatively simple. Hand-coating resin onto the fabric requires less specialized equipment. The lay-up and curing steps are straightforward, allowing for quicker production times. This simplicity makes wet carbon fiber accessible to a broader range of manufacturers.
Disadvantages
Variability in Quality
Wet carbon fiber often exhibits variability in quality. The hand-coating technique can lead to inconsistent resin distribution. This inconsistency results in weak points within the material. Air bubbles frequently form during the resin application. These bubbles create voids that compromise structural integrity. Wavy fiber weaves also occur, further reducing the material’s strength. Industries requiring high precision and reliability may find these inconsistencies problematic.
Potential for Resin Waste
The wet carbon fiber process has a higher potential for resin waste. Manual resin application can lead to excess resin usage. This excess increases material costs and environmental impact. The lay-up process may result in uneven resin distribution. Uneven distribution necessitates additional resin to fill gaps, leading to further waste. Efficient resin use becomes challenging, impacting overall production efficiency.
Comparative Analysis
Performance Comparison
Strength
Dry carbon fiber demonstrates superior strength due to its uniform resin distribution. The pre-impregnation process ensures each fiber receives an even coating of resin. This results in fewer weak points within the material. Wet carbon fiber, on the other hand, often exhibits variability in strength. The hand-coating technique can lead to inconsistent resin application. This inconsistency creates potential weak spots.
Durability
Dry carbon fiber offers exceptional durability. The vacuum-sealed curing process eliminates air bubbles and ensures an even resin distribution. This results in a material with high structural integrity. Wet carbon fiber may suffer from reduced durability. Air bubbles and uneven resin distribution can compromise the material’s longevity. Industries requiring long-lasting performance often prefer dry carbon fiber.
Cost Comparison
Initial Investment
The initial investment for dry carbon fiber is significantly higher. The pre-impregnation process requires specialized equipment and high-quality materials. The vacuum-sealed curing process adds further to the cost. Wet carbon fiber presents a more cost-effective option. The hand-coating technique uses cheaper materials and equipment. This affordability makes wet carbon fiber attractive for budget-conscious projects.
Long-term Costs
Long-term costs for dry carbon fiber can be lower despite the high initial investment. The material’s durability and consistent quality reduce maintenance and replacement expenses. Wet carbon fiber may incur higher long-term costs. Variability in quality can lead to frequent repairs and replacements. Industries must weigh initial savings against potential future expenses.
Application Suitability
Industry-specific Uses
Dry carbon fiber suits industries demanding high performance and reliability. Aerospace and automotive sectors benefit from its superior strength and durability. Wet carbon fiber finds applications in less critical areas. Industries such as sports equipment manufacturing and general consumer goods often use wet carbon fiber. The flexibility in resin application allows for custom designs and complex shapes.
Customization Needs
Wet carbon fiber offers greater customization options. The hand-coating method allows for adjustments in resin quantity. This flexibility accommodates unique shapes and tailored solutions. Dry carbon fiber provides limited customization. The pre-impregnation process restricts adjustments in resin application. Industries needing specific designs may prefer wet carbon fiber for its adaptability.
Practical Applications
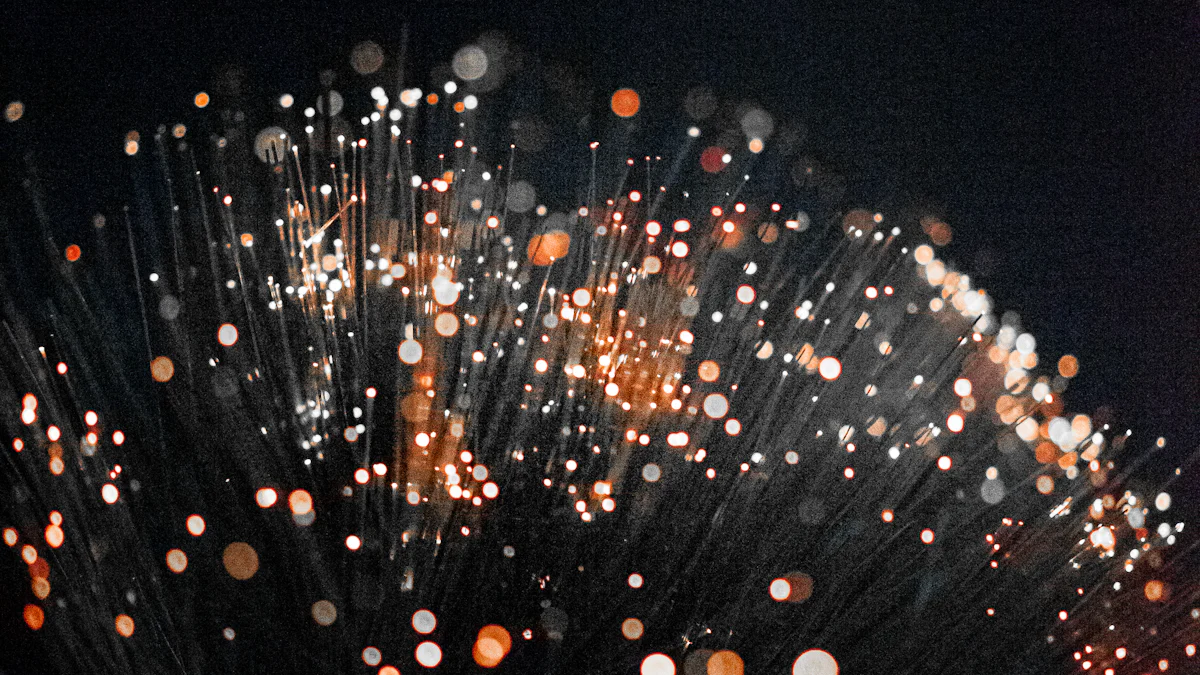
Automotive Industry
High-performance Vehicles
High-performance vehicles benefit significantly from carbon fiber aero components. Dry carbon fiber’s superior strength-to-weight ratio enhances vehicle performance. Manufacturers use dry carbon fiber for structural parts like chassis and body panels. This material reduces weight, improving acceleration and handling. The consistency in quality ensures reliable performance under high stress.
Everyday Cars
Everyday cars also incorporate carbon fiber aero parts to improve fuel efficiency and safety. Wet carbon fiber offers a cost-effective solution for non-critical components. Manufacturers use wet carbon fiber for interior trims and exterior panels. The flexibility in resin application allows for custom designs. This adaptability suits the diverse needs of everyday car models.
Aerospace Industry
Commercial Aircraft
Commercial aircraft rely on carbon fiber aero materials for lightweight and durable components. Dry carbon fiber’s uniform resin distribution provides exceptional strength. Aircraft manufacturers use dry carbon fiber for wings, fuselage sections, and control surfaces. This material reduces overall weight, leading to improved fuel efficiency and lower emissions.
Spacecraft
Spacecraft demand materials that withstand extreme conditions. Dry carbon fiber meets these requirements with its high strength and durability. Spacecraft manufacturers use dry carbon fiber for structural elements and protective shields. The vacuum-sealed curing process ensures minimal defects, crucial for space missions. Wet carbon fiber finds limited use in spacecraft due to potential variability in quality.
Sports Equipment
Bicycles
Bicycles made from carbon fiber aero materials offer superior performance. Dry carbon fiber’s lightweight properties enhance speed and maneuverability. Manufacturers use dry carbon fiber for frames and forks, ensuring high stiffness and strength. Wet carbon fiber provides an affordable option for less critical parts like seat posts and handlebars.
Sporting Goods
Sporting goods manufacturers leverage carbon fiber aero materials for various products. Tennis rackets, golf clubs, and hockey sticks benefit from dry carbon fiber’s consistent quality. The material’s high tensile strength improves durability and performance. Wet carbon fiber offers flexibility for custom designs in sporting goods. This adaptability suits products requiring unique shapes and specifications.
Dry and wet carbon fiber exhibit distinct characteristics. Dry carbon fiber offers higher strength, lighter weight, and consistent quality due to the autoclave process. Wet carbon fiber provides cost-effectiveness, flexibility, and suitability for complex shapes.
Selecting the appropriate type of carbon fiber depends on specific application needs. Industries requiring high performance and reliability should consider dry carbon fiber. Budget-conscious projects and those needing custom designs may benefit from wet carbon fiber.
Careful consideration of industry requirements and specific needs will guide the optimal choice between dry and wet carbon fiber.
See Also
Choosing Top Carbon Fiber Aerodynamic Components for Your Vehicle